Wood Moulding Solutions for Manufacturers & B2B Buyers
Arnold Wood Turning specializes in custom wood moulding and dimension components made exactly to your specifications. We focus on industrial and manufacturing applications – not decorative home trim – delivering wood parts in bulk production runs with consistent quality.
If you need finely milled mouldings or cut-to-size blanks, our team provides precision-crafted wood components in hardwood or softwood, in virtually any size, shape, or profile your business requires.
Custom Wood Mouldings Made to Specification
Our wood mouldings and dimension blanks are crafted to meet your exact needs. “Dimension” components refer to any cut-to-size wood blanks (solid or laminated) needed for your product. This means we can supply simple square or round stock for further processing, as well as intricately profiled mouldings ready for use.
Every piece is cut, molded, or even lathe-turned with precision so that it fits into your assembly or product line. We welcome orders for production-run quantities so you have a reliable supply of parts for as long as you need them.
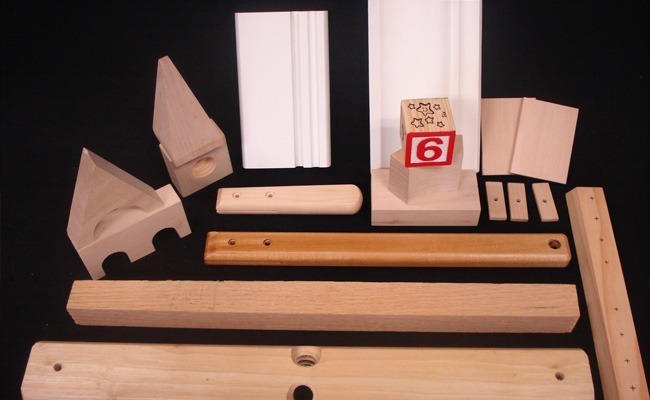
Custom Wood Mouldings and Dimension Components for Bulk Manufacturing
Precision-crafted wood mouldings and dimension parts customized for bulk manufacturing and specialty applications.
Industrial Applications of Our Wood Mouldings
Our moulded wood components are used across a wide range of industrial and commercial applications. Here are just a few areas where our wood mouldings excel:
• Tools & Equipment: Sturdy wooden parts for tools and hardware. For example, we produce brush blocks for industrial brushes and custom wooden housings or spacers for machinery. Many tool manufacturers integrate our mouldings into handles, grips, or structural supports.
• Packaging & Crating: Durable wood mouldings used in packaging, shipping, and storage. We supply slats, compression sticks, and custom-cut strips that provide support and protection in crates and pallets. These components add strength and keep contents in place.
• Machinery & OEM Components: Machine manufacturers and OEMs incorporate our wood parts into equipment and assembly lines. We’ve made wooden loom pieces for textile machinery, precision-cut guides and stops for industrial machines, and other specialty components where wood’s properties (such as non-conductivity) are essential.
• Sporting Goods & Recreation: We produce wood mouldings for the sporting and recreation industry. Manufacturers of outdoor play structures use our wooden climber rungs and support bars. We also supply lathe-turned mouldings for items like billiard cue components, bat or mallet blanks, and other sports or game pieces that demand strength and consistency.
• Furniture & Product Manufacturing: Many furniture makers and product manufacturers rely on our moulded wood components as part of their designs. We supply chair or table frame parts, furniture dowels and rails, and other custom profiles used structurally in furniture.
If you require a wood component with a specific profile or shape, chances are we’ve made something similar, and we can craft a solution for you, too.
Bulk Production with Consistent Quality
When you partner with us, you can count on consistent quality at scale. We specialize in bulk orders and high-volume production runs and our production process is optimized for efficiency and repeatability. Your wood mouldings will be uniform, shaped, and finished.
Every batch of mouldings undergoes inspection so that only top-quality pieces make it to your loading dock. We use quality hardwoods and softwoods to minimize defects and warping, which gives you components that are reliable and long-lasting. Plus, our decades of experience in woodworking mean we know how to maximize yield and maintain quality.
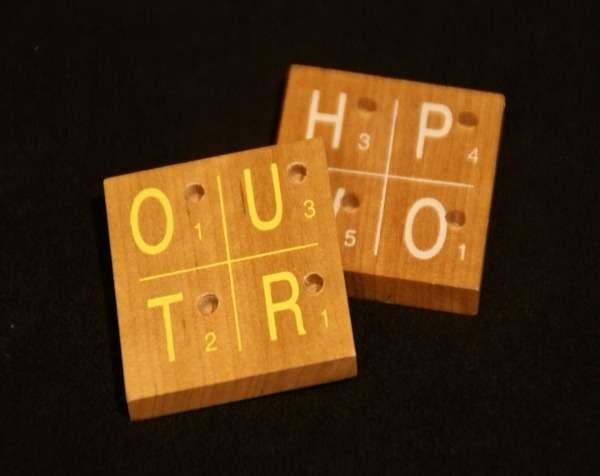
Bulk Wooden Game Parts for Large-Scale Manufacturing
Bulk wooden game parts designed for high-volume production. Custom drilling, silk-screening, and finishing options available to meet manufacturing requirements.
Custom Machining & Secondary Operations
We offer a full range of custom machining and secondary operations to deliver wood components that are ready to use upon arrival. Rather than sending you plain cut wood, we can incorporate all the extra features your part needs, saving you time and effort in your own facility.
Our advanced workshop includes both multi-spindle moulders and precision lathes, so we can create everything from standard straight-profile mouldings to complex lathe-turned shapes and cylindrical parts.
By handling these secondary operations in-house, we ensure that each modification is done with precision and that all components remain consistent. Your parts will arrive fully machined and ready to integrate.
Wide Selection of Wood Species & Grades
Different applications call for different materials, and we offer a wide selection of wood species to choose from. We can source and machine the ideal wood for your project.
If you have a specific wood species requirement or need to match an existing material, just let us know. We can often accommodate special requests and will work with you to find the best material that balances performance with cost.
Why Partner with H. Arnold Wood Turning?
Choosing the right supplier for your wood mouldings is important. Here’s why manufacturers and distributors have trusted Arnold Wood Turning for over a century.
We’ve been in the wood products business since 1919, giving us unmatched experience in wood manufacturing. We’ve honed our craft and tackled nearly every type of wood component imaginable. When you work with us, you get a partner who understands wood engineering inside and out.
Unlike small suppliers, we are fully equipped for high-volume production. We handle large orders and repeat runs efficiently, so you won’t face delays or inconsistencies. We know how to scale production while maintaining quality.
We thrive on custom projects and will work with you to make it happen. Our team can assist in refining designs for manufacturability, and we’re happy to produce prototypes or small trial runs before full production.
From material selection to final inspection, quality is our priority. Our team makes sure each piece meets your specifications and our high standards.
Arnold Wood Turning is a one-stop shop for wood components. We can do it all – sourcing the lumber, cutting, turning, shaping, finishing, and even light assembly. You don’t have to juggle multiple vendors for different steps. We simplify your supply chain by delivering a complete product, allowing you to focus on your business.
Ready to Get Started? Request Your Free Quote Today
If you’re looking for a reliable partner to supply high-quality wood mouldings in bulk, we’re here to help. We invite manufacturers, distributors, and businesses of all sizes to reach out and discuss your project with our friendly experts.
Contact us today for a free, no-obligation quote on your custom wood moulding needs. Our team will gladly talk through your requirements, offer guidance on materials and design, and provide a prompt estimate to get your project moving forward.